Service Scope
Nine Key Processes of Industry 3.0 to Industry 4.0
NexAIoT provides solutions based on the iAT2000 Cloud SCADA System, assisting customers in building intelligent operation and management of manufacturing factories. NexAIoT offers smart manufacturing consulting services that support customers in investigating the current status of the factory and evaluate the current factory automation level. The practice provides evaluation reports and solutions for upgrading Industry 4.0. The process is divided into nine stages; they are:
- Industry 3.0 stage: EtherCAT Machine Automation
- Industry 3.1 stage: Production Line Monitoring Automation
- Industry 3.2 stage: Industrial Robot Process Automation
- Industry 3.3 stage: Edge Computing for Device Connectivity and Automation
- Industry 3.4 stage: Production Information Management by Cloud Service
- Industry 3.5 stage: ERP/MES/SCADA Integrated and Real-time Decision Making System
- Industry 3.6 stage: Digital Headquarter for Distributed Factories Operation
- Industry 3.7 stage: Digital Transformation Enterprise and MASA
- Industry 3.8 stage: Digitized and AI-enabled Manufacturing Services
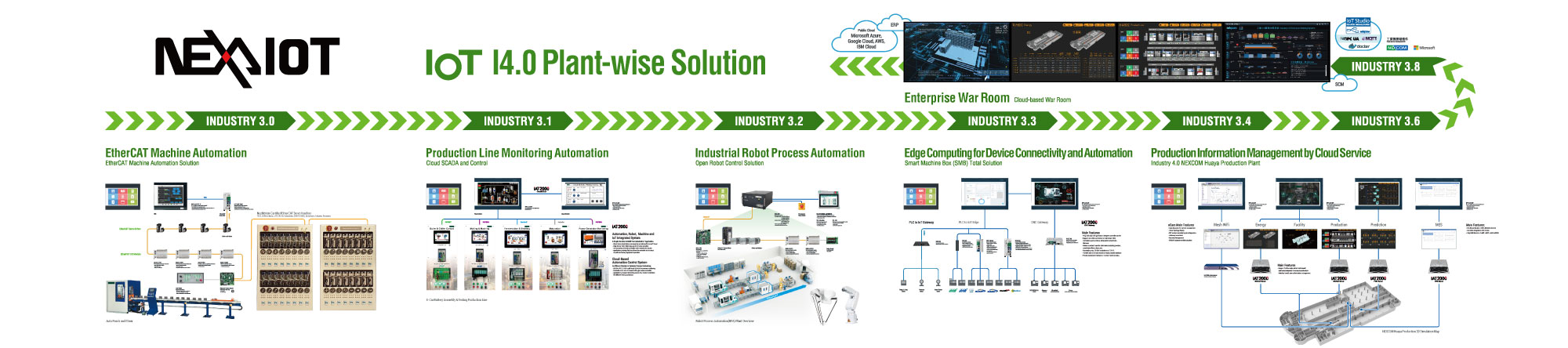
Industry 3.0 Stage: EtherCAT Machine Automation
In the first stage, the main task to upgrade labor-based manufacturing plants, old machines, and original equipment manufacturers (OEM) with open motion controllers based on high-speed EtherCAT technology, software-defined motion control algorithms, and high-speed performance drives/motors, encoders, counters, and large-size touch screens. The upgrade process is implemented with senior mechanism and electronic control engineers, interview customized machine customization services to develop non-standard production machines for various industries. The targeted goal of Industry 3.0 stage is to assist customers in the planning, design, development, and transformation of non-standard production machines in terms of mechanism, electrical control, and process to improve product production efficiency, productivity, and stable quality. More importantly, through the customization of software development, Industry 3.0 can provide more diversified and complex motion control to shorten the time to market while reducing development costs.
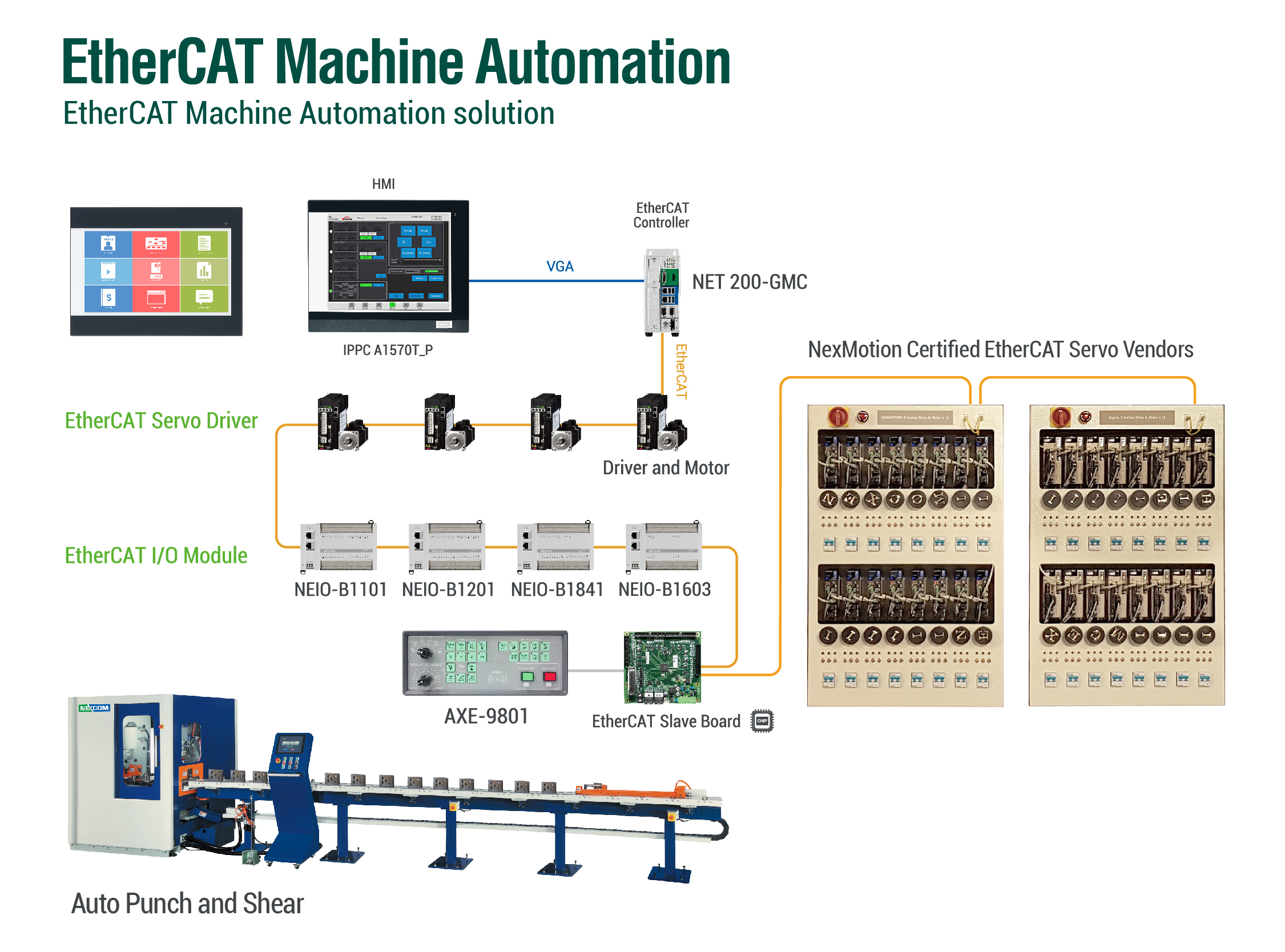
- EtherCAT multi-axis motion controller: NIFE200, NIFE300-GMC32
- Browser-based HMI:IPPC Series & JMobile Runtime PC
- Distributed I/O: NEIO Series, Yaskawa VIPA SLIO Series
- EtherCAT drive control integration solution: Yaskawa Sigma 7 Series, Shihlin Electric SDP Series
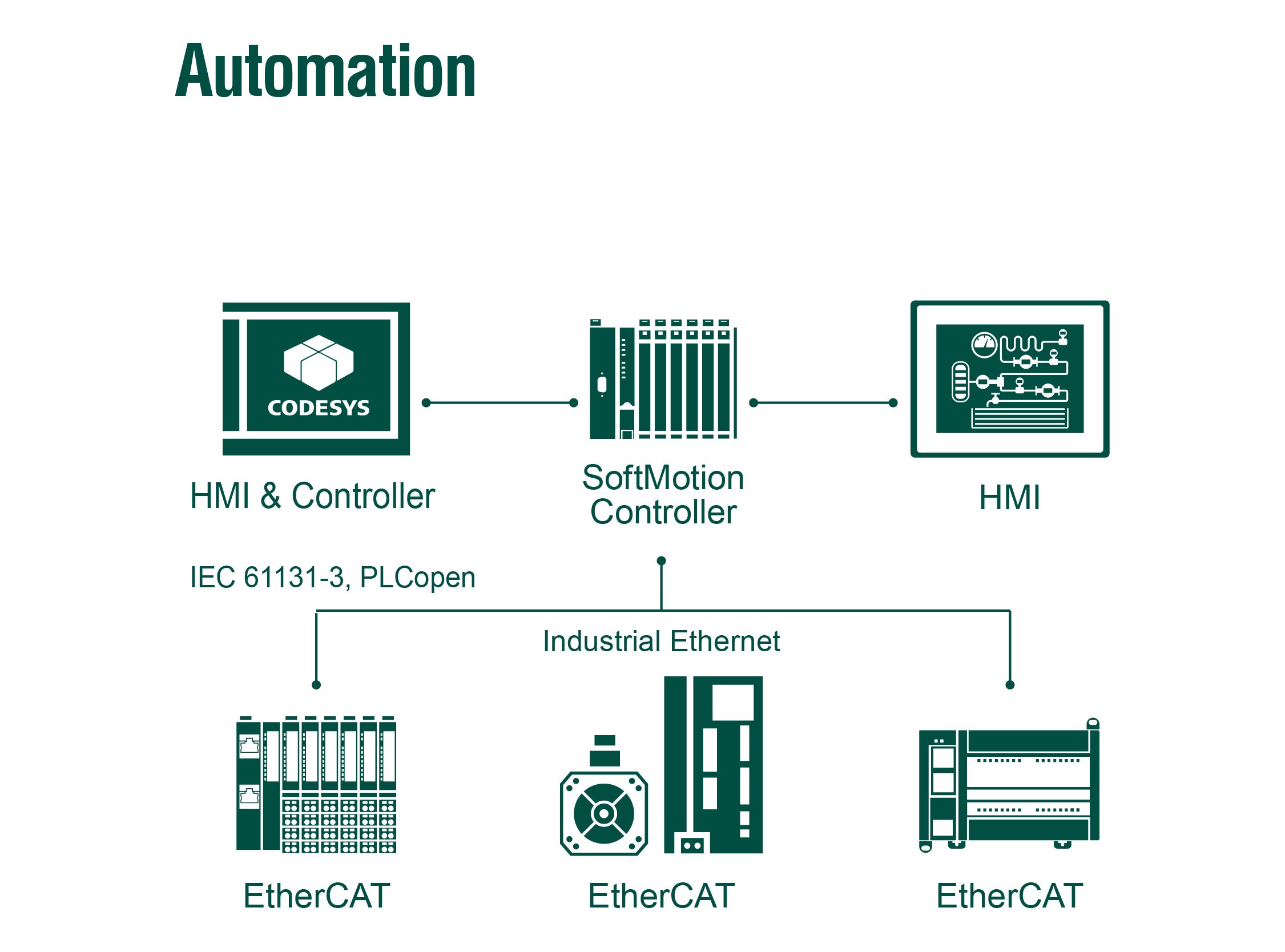
Industry 3.1 Stage: Production Line Monitoring Automation
In the second stage, the goal is to upgrade all kinds of non-standard automated machines, production equipment, factory monitoring sensors, and process instruments in the existing manufacturing plants. The physical quantity of consumed oil, gas, water, electricity, plus production line information and other values are automatically collect in the central control room by the iSCADA graphic control visualization software through the communication protocol. The graphical whole-plant monitoring screen of iSCADA provides real-time production status, alarm prompts, and historical data queries. Senior Automation Project Consultants conduct on-site surveys and then use the iAT2000 Cloud Intelligent System to prepare the line monitoring automation upgrade evaluation, provide system integration engineering services, and build the automatic monitoring system without manual meter reading. The objective of Industry 3.1 is to operate the factory with a reduced overall cost of ownership.
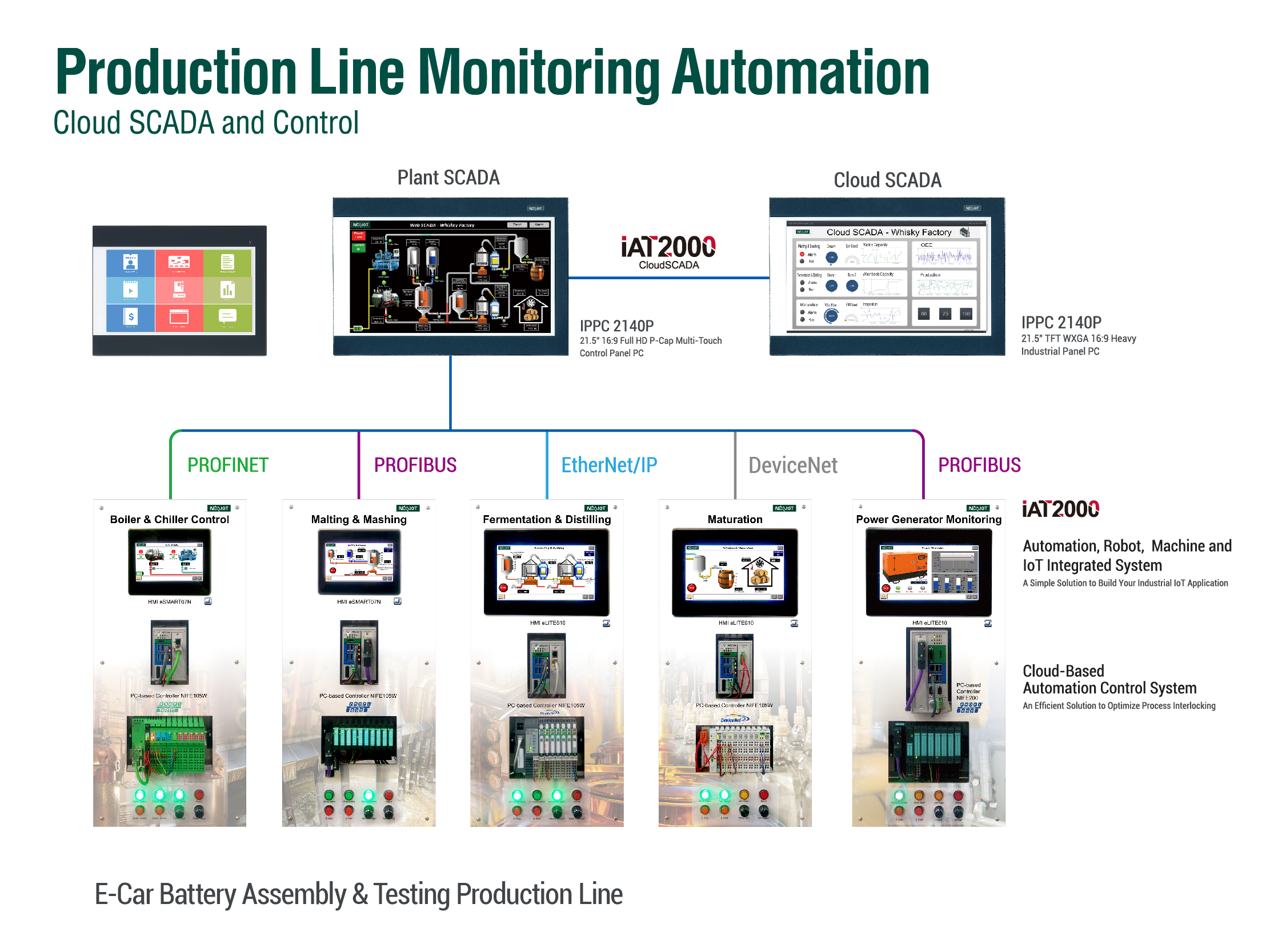
- SCADA: NISE3800-iSCADA Series
- PC-based PAC: NIFE Series
- HMI: IPPC Series & JMobile Runtime PC
- Distributed I/O: Yaskawa VIPA SLIO Series
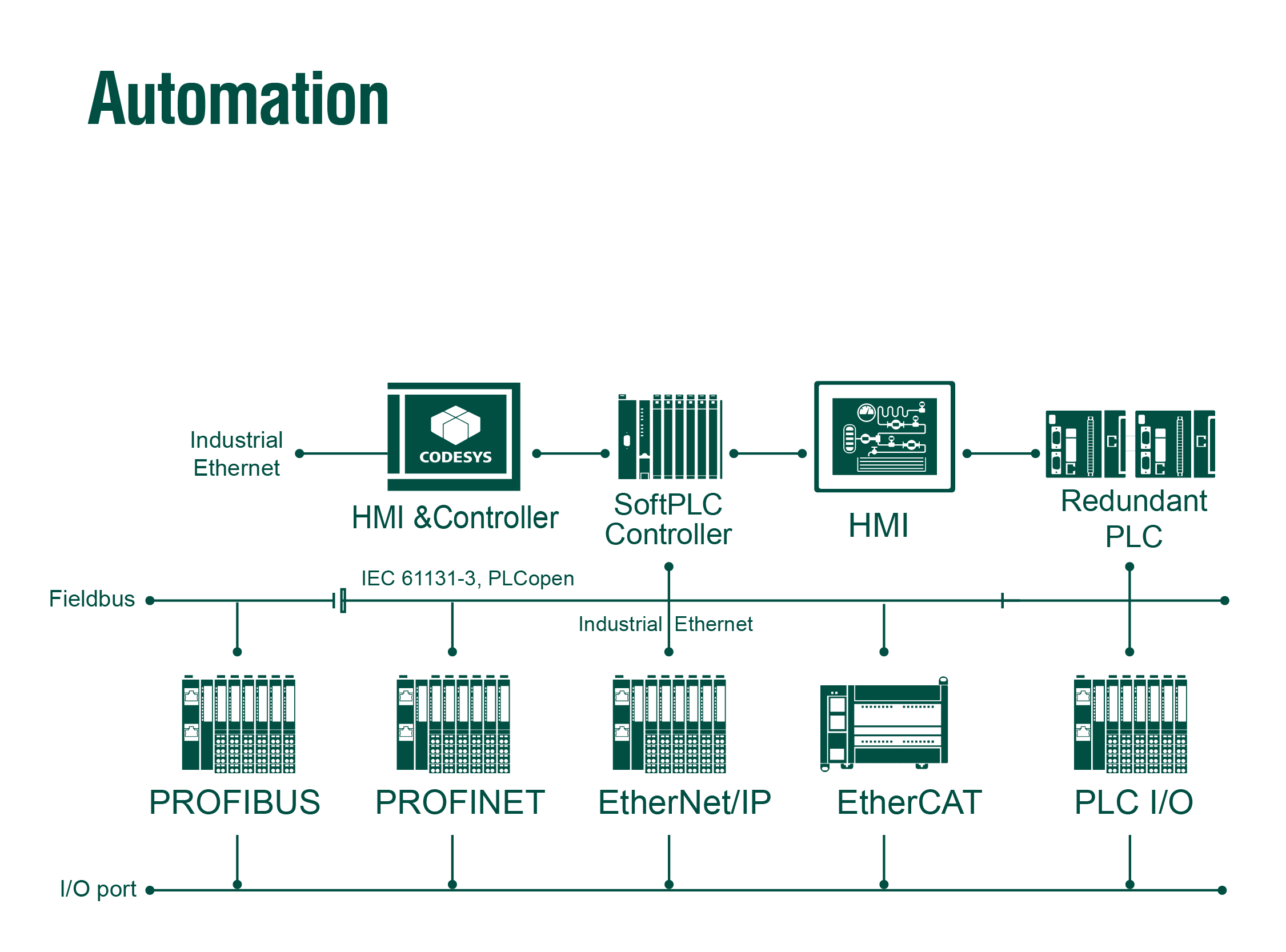
Industry 3.2 stage: Industrial Robot Process Automation
In the third stage, the focus of the upgrade of the manufacturing plant is to use industrial robots to perform repetitive, streamlined station operations, and perform high-load, high-precision, and high-speed tasks that cannot be completed by humans. For assembly and processing operations with high space complexity, the 7-axis collaborative robot arm can be used to assist the operator in reducing the complexity and time and the production output and efficiency. By integrating the machine vision system, more diverse unmanned handling, positioning, processing, and other operations can be accomplished. Through application interviews and on-site investigations by senior robotic automation engineers, with the iRAP2000 intelligent robot solution, the production line, machine & robot automation integration benefit evaluation, and system integration engineering services are provided to build a high-efficiency robotic automation manufacturing line.
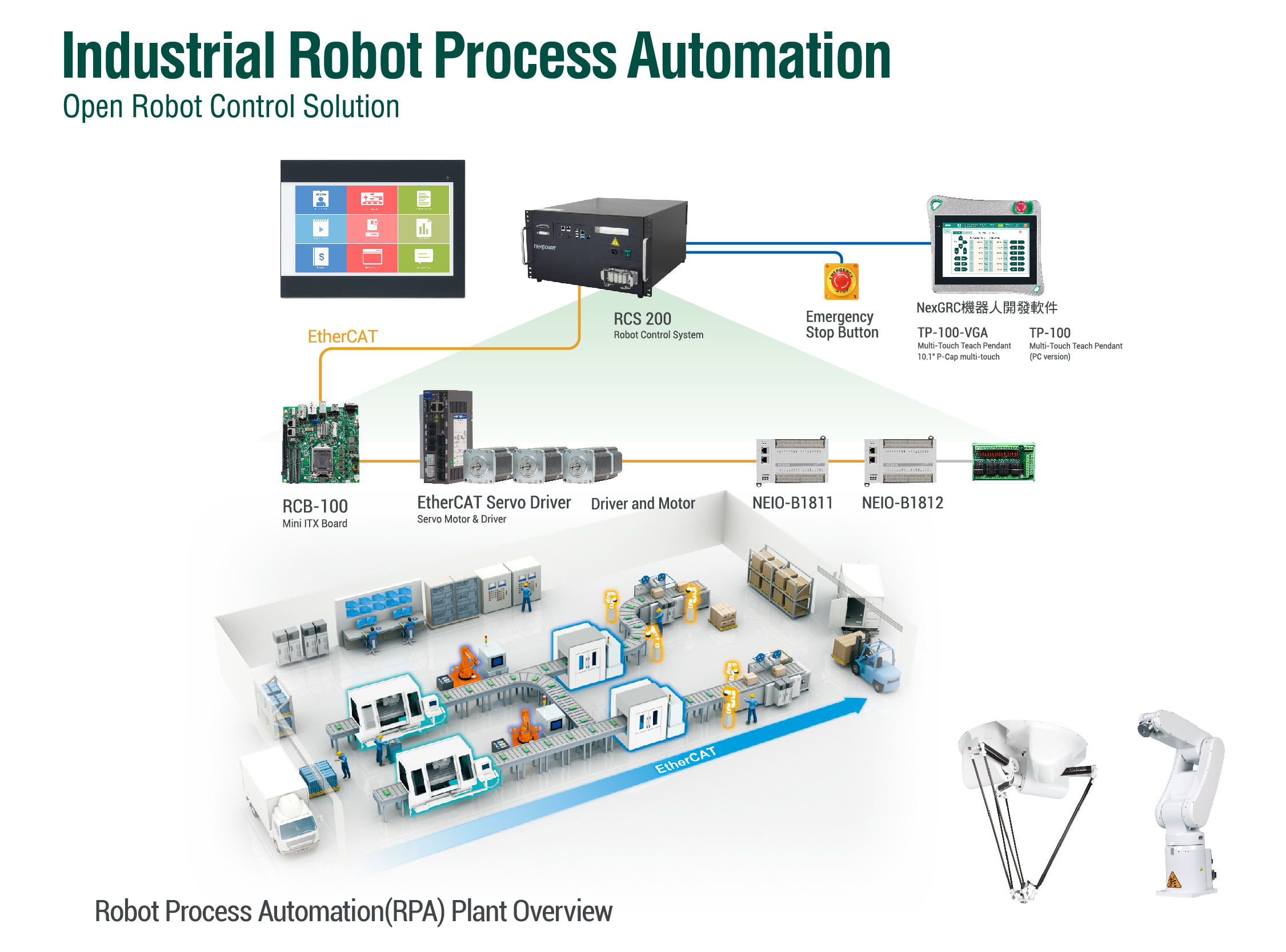
- Robot Controller: RCS Seriese
- Embedded Motherboard: RCB-100
- Robot Teach Pendant: TP-100
- Distributed I/O: NEIO Series
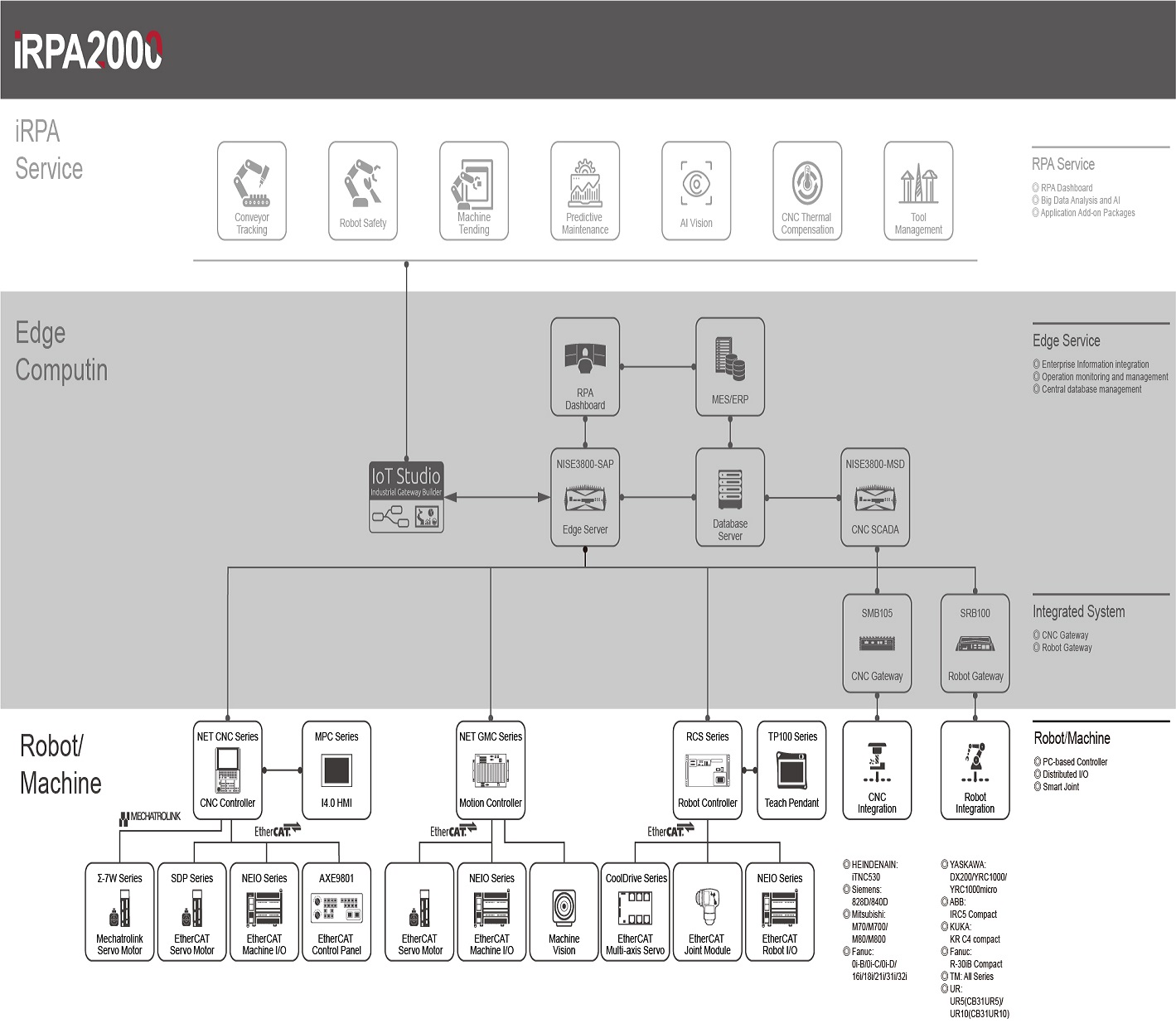
Industry 3.3 Stage: Edge Computing for Device Connectivity and Automation
In the fourth stage, the upgrade’s emphasis is to give a highly automated manufacturing the factory digital management and application. The initial step is to use intelligent IoT gateway solutions to integrate the automation equipment of each independent island in the manufacturing factory, such as production machines, CNC, and robots, then built them as digital twins. The upgrade also aims to complete comprehensive equipment networking and collect production information of on-site processing machines. The PLC to IoT Gateway and Edge Server within the built-in IoT Studio and IoT integration software will manage all manufacturing information and perform ETL data cleansing. A multi-functional dashboard can be designed to present the analyzed KPI as a visual production management system and allows a two-way data transmission with SCADA, SFC, or other methods to develop a management system on the production site, and then operate with the enterprise system convergence. The senior automation project consultants and management consultants collaborate to conduct field equipment surveys and management demand interviews and propose manufacturing management recommendations via the iAT2000 Cloud Intelligent System. The dream team provides system integration engineering services to build digitally managed manufacturing plants.
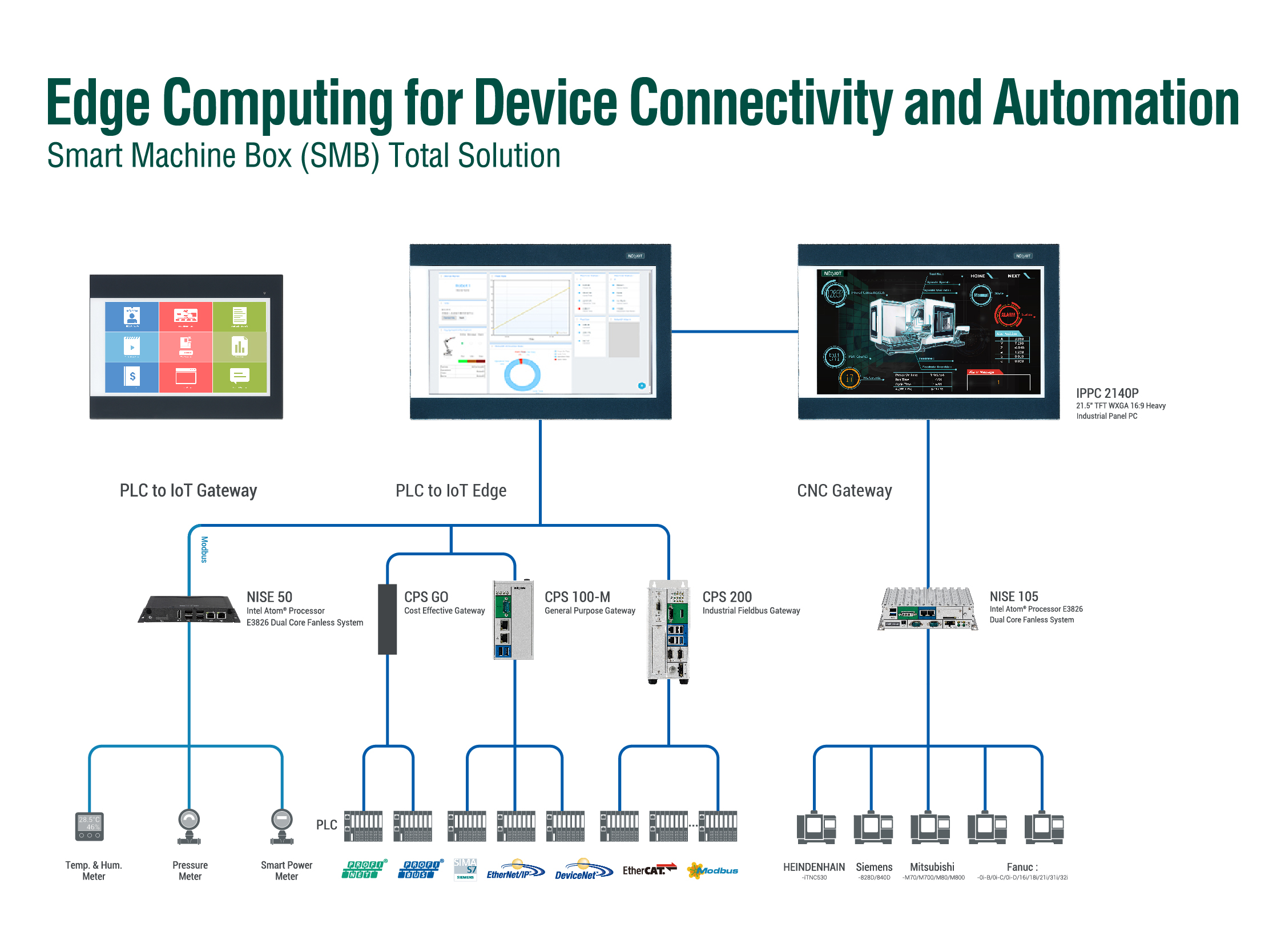
- Edge Server: NISE3800-Edge
- PLC to IoT Gateway: CPS Series
- CNC Gateway: NISE105-CNC Series
- Robot Gateway: SRB Series
- Non-protocol Gateway: VIC7000 Series
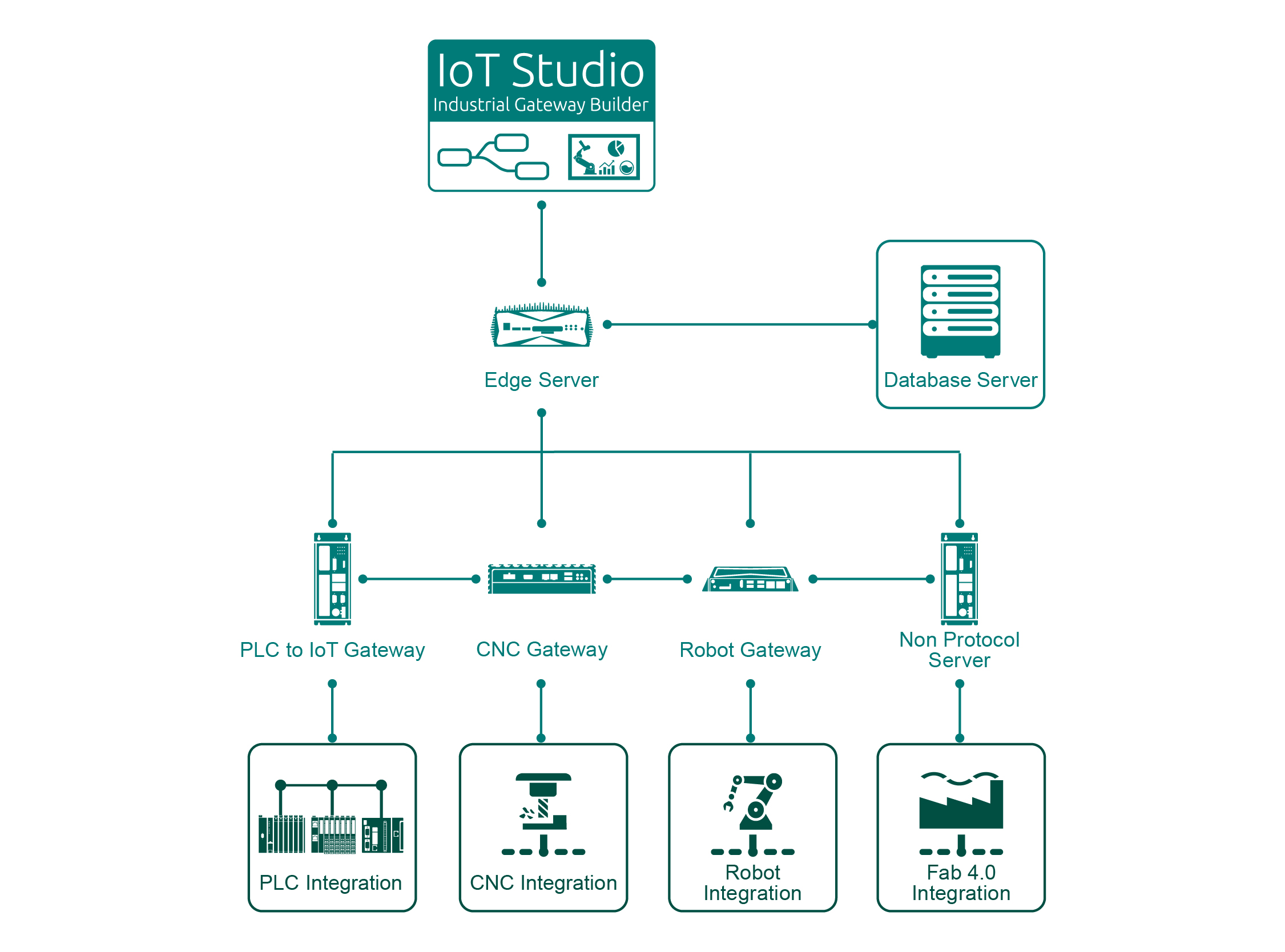
Industry 3.4 stage: Production Information Management by Cloud Service
In the fifth stage, the primary mission of the upgrade is to build a digital manufacturing factory with a smart factory infrastructure. As the foundation of production management, this infrastructure is capable of developing various management systems with production equipment management, production history tracking, production line, and equipment KPI monitoring dashboards. In response to the needs of customer information tracking, production capacity/utilization rate maximization, production & process information analysis, the above management dashboard is developed via the built-in IoT Studio IoT integration software PLC to IoT Gateway and Edge Server. When production equipment is expanded, new factories are multiplied, and external customers need to track the production progress and production history, the storage of information will continue to increase. Through the application of external information exchange, geographically distributed equipment, and cross-factory production line management, the data received by the IoT Gateway/Edge Server can be transmitted to the mainstream public cloud. These are the benefits of the flexible expansion of cloud services and centralized management of digital factories. The implementation of this solution requires an on-site survey conducted by a Senior Factory Automation Project Consultant. Also, a Cloud System architect will join the project consultant to provide a production management information cloud evaluation using the integrated system and Edge Service. The Industry 3.4 solution provides OT/IT/IoT/Cloud integrated turn-key engineering services to create a company-specific digital factory.
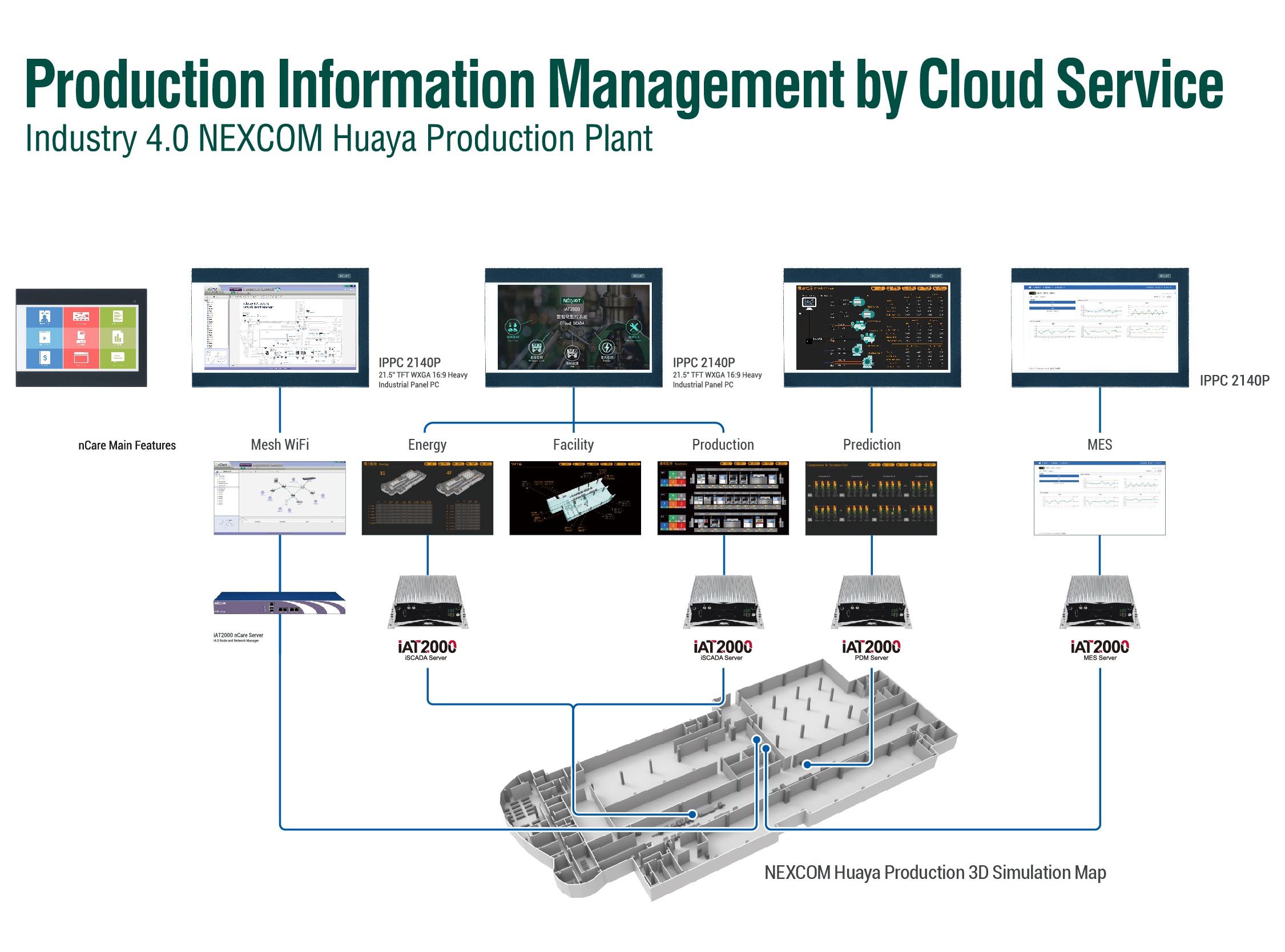
- Edge Server: NISE3800-Edge & IoT Studio
- PLC to IoT Gateway: CPS Series & IoT Studio
- Mesh WiFi: IWF Series & nCare Software Suite
- SCADA System: FMCS, EMS
- MES: Production Line Management
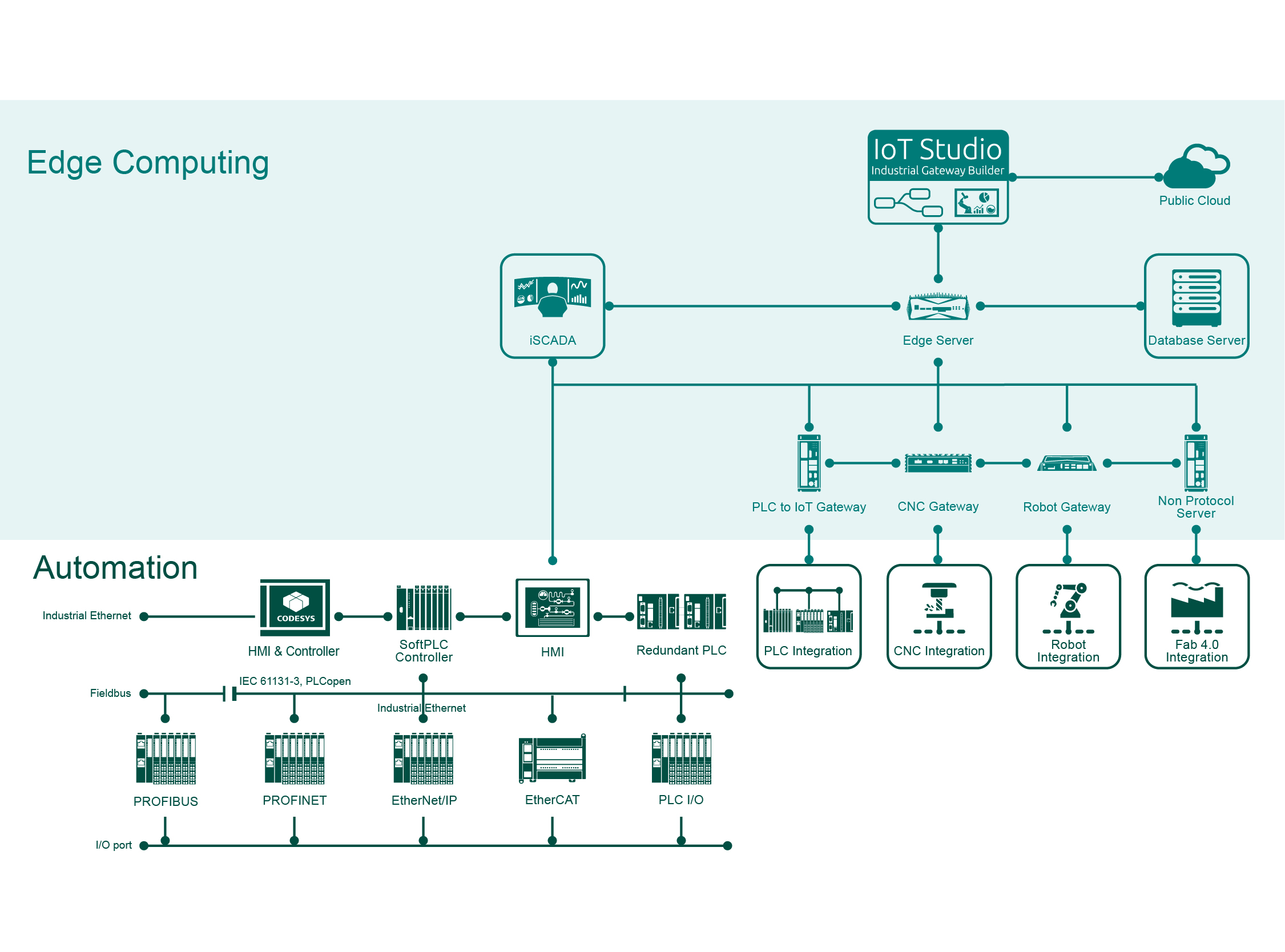
Industry 3.5 stage: ERP/MES/SCADA Integrated and Real-time Decision Making System
The focal point of the upgrade in the sixth stage is to build an OT/IT integrated smart manufacturing enterprise. The digital factory built with iAT2000 integrates the information systems required for business operations. The sources of information include MES, WMS, ERP, and other systems, include the steps of receiving orders, confirming the status of various resources with ERP and WMS, finalizing production schedules and current production capacity with MES, and the delivery date of the final reply to the order. This data-driven decision-making reference offers the management personnel (CEO, plant manager, and business director) and operating personnel at all levels to achieve accurate delivery, asset utilization optimization, visibility of management performance, and improved corporate profits, etc.The implementation of this solution requires an Enterprise Architect to conduct management requirements interviews, and then a Senior Plant Automation Project Consultant to conduct on-site surveys. The iAT2000 Cloud Intelligent System will be utilized to present a digital factory implementation report. And the OT/IT system integration Engineering services will be provided to build a company-specific digital factory that complies with open architecture and international standards.
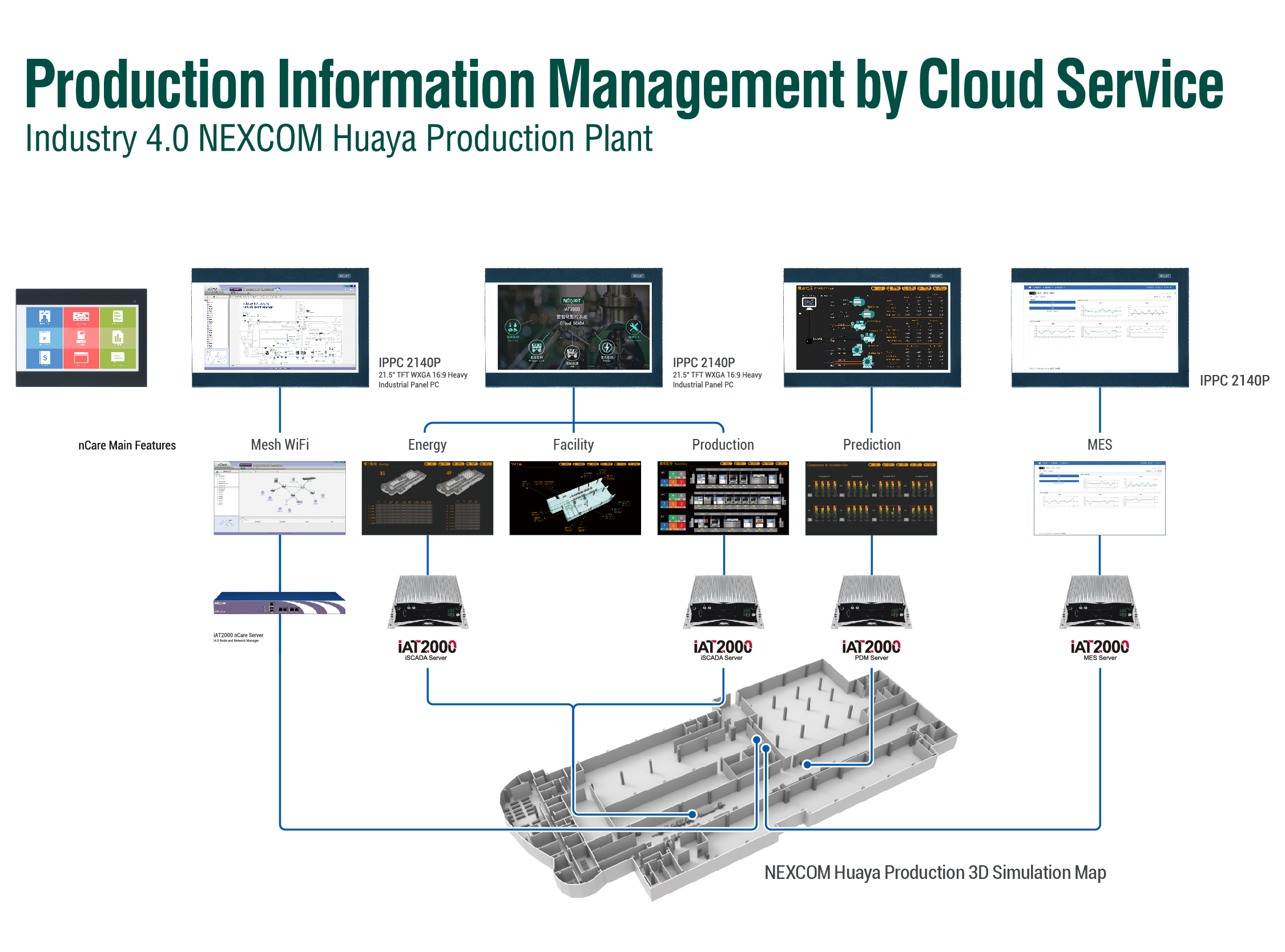
- SCADA: NISE3800-iSCADA Series
- SAP Edge Server: NISE3800-SAP & IoT Studio
- IT System: ERP/MES
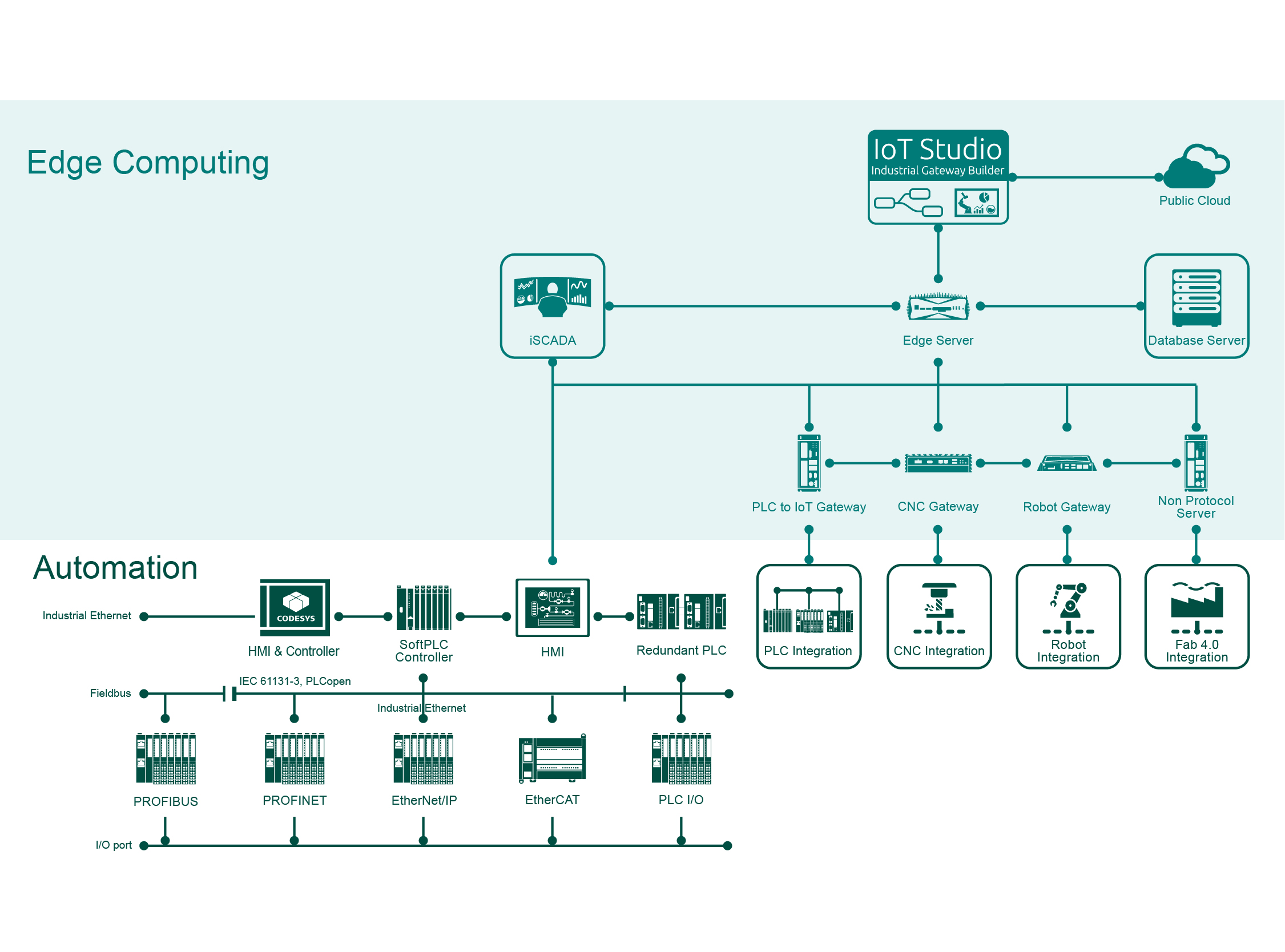
Industry 3.6 stage: Digital Headquarter for Distributed Factories Operation
In the seventh stage, the essential undertaking of this upgrade is to arrange digital factories that already had smart factory infrastructure to deploy the digital headquarters with an enterprise war room. The visual system of the war room connects the vital operation information between the digital chemical factory and the enterprise, and it presents the core data for real-time operational decisions through the matrix monitor wall. The information sources of the visual system include SFC, SCADA, MES, APS, CIM, WMS, ERP, SCM, CRM, and other systems, and the geographically dispersed manufacturing plants are seamlessly integrated. The industry 3.6 solution seizes the key KPIs of each system in real-time, develops management modules, schedules production capacity with virtualization, adjusts resources dynamically, and increases profits. The establishment of this solution requires an Enterprise Architect to conduct management demand interviews, and then a Senior Plant Automation Project Consultant to conduct on-site investigations. The iAT2000 cloud intelligent system will be used to present the Enterprise War Room implementation report, and OT/IT System integration engineering services will be offered to create a real-time Enterprise War Room with digital factory information and corporate information.
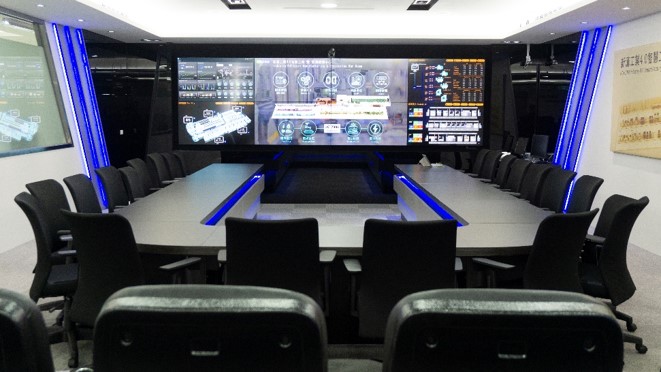
- OT SaaS: FMCS
- OT SaaS: Production Line Management
- OT SaaS: Predictive Maintenance
- OT SaaS: EMS
- IT SaaS: iPDM
- 6. IT SaaS: ERP/MES
- 7. IT SaaS: NexWMS
- 8. IT SaaS: iQC
- 9. IoT SaaS: Mesh WiFi
- 10. IoT Security SaaS : eSAFE
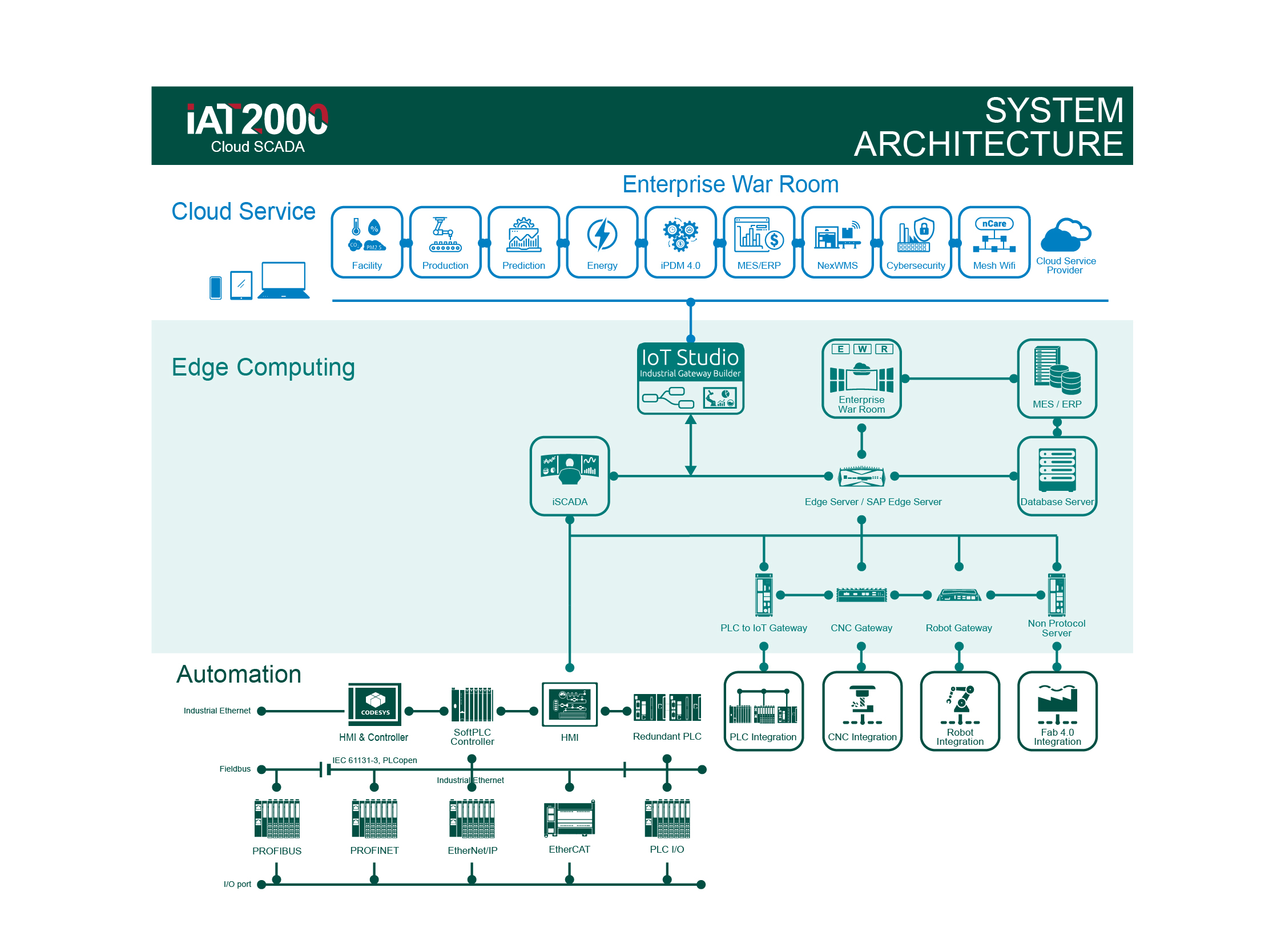
Industry 3.7 Stage: Digital Transformation Enterprise &IT Middleware Platform
Industry 3.8 Stage: Digitized and AI-enabled Manufacturing Services
In the eighth stage, the concentrated assignment of the upgrade is to use the Mesh Applications Service Architecture of the OT/IT management modules and their functions in the Enterprise War Room to build various microservices required for intelligent manufacturing. The management modules store and manage data in the form of data lakes. The data sources include digital twin-structured machines, equipment, assets, systems, management modules, etc. Open RESTful API is used as an interface for open data and functional use among microservices to develop business intelligence applications. NexAIoT researched and developed a data platform for intelligent manufacturing. Through the iAT2000 technology platform, the data from the digital factory is connected to the data platform built with SAP Edge Server, where CRM, ERP, PLM, SCM, WMS, EDA, CIM, MES, QC, SCADA, FMCS, EMS, Production Line Management, and SFC can be seamlessly integrated. NexAIoT’s data platform opens up the channels between the OT and IT systems. All operating information and data use enterprise architects to import the management methodology. Data analysts are utilized to examine the cause and effect of operation problems through the machine learning platform and construct the machine learning or mathematical models. The data platform predicts potential corporate risks and then ensures the company is profitable with positive numbers to complete digital transformation and borderless smart manufacturing. NexAIoT has a full range of team experts, including senior plant automation project consultants, senior management consultants, data scientists, and OT/IT system integration teams. iAT2000 Cloud Intelligent Solutions are designed to find cross-system operational insights through data, and they assist enterprises to create an exclusive Industry 4.0 smart manufacturing factory.

